Why is traceability important?
As the agricultural sector intensifies and food is shipped globally, food safety is becoming a major concern. Where does our food come from? How can consumers trust food that is produced far away from their homes, often in countries where legislation regarding for example, the use of pesticides is absent, or enforcement is weak?
Measuring residue levels of agrochemicals or microbiological contamination in the final product can be done to some extent but is a huge additional cost and often a burden for the environment. Therefore, the focus in the food industry has always been on process control. Where in the process could something go wrong? By mapping the process and analyzing the food safety hazards, these can be reduced. This process is commonly known as HACCP, which stands for Hazard Allowance Critical Control Points.
Scenario
For example, when engine oil is transported on the back of the same truck that is used to carry sacks of cocoa beans, this could easily result in contamination of the cocoa throughout the cocoa value chain. Traces on mineral oil can end up in the chocolate bar. In fact, as detection methods improve constantly, large industrial companies, such as Nestle, Ferrero Rocher and Mars, do check for residues of pesticides.
As detection methods improve it is possible to raise the bar, but also the costs… Mineral oil contaminations, or MOSH/MOAH, are forming a huge challenge and they could not easily detect low contamination levels until recently. However, checking the contamination in the raw material, at the buying centers, for example, would only partially assist to reduce contamination risks.
It is important to be able to trace the contamination backwards in the chain. In other words; trace the produce from the factory, to the farmer cooperative, to the bag, to the collection centre, to the farmer and his or her field that the cocoa beans came from. This is where the more challenging part starts.
A fully traceable supply chain
eProd offers an affordable Supply Chain Management system for agribusinesses and cooperatives. The system manages many aspects of the supply chain, such as farmer registration, field inspections, collections, training, communication, (mobile) payments, etc. It also manages product traceability! Through a combination of a mobile app, which is used by extension workers in the field and a desktop application, which is used by an administrator of the agribusiness, eProd can create a traceable product from field to warehouse, factory or packhouse.
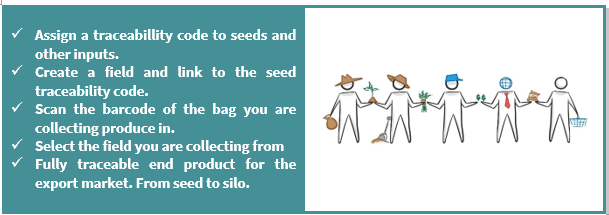
How does it work?
To understand where the product comes from, it is important to understand the process workflow and the data that is collected throughout the workflow. This requires documentation and tools to manage this. With eProd, data collection starts in the field by creating a profile for a farmer and registering his or her fields.
A unique Field ID will be assigned to the field based on the Farmer ID and the date of registration. Let’s take the example of aa sorghum farmer with Farmer ID CF1810266. In this case CF stands for Contract Farmer, 18 for the year 2018, 10 for the month October and 266, for the 266th farmer registered in that month. The Field ID consists of Farmer ID (CF1810266) + crop (e.g. SGM) + date (0720) = CF1810266SGM0720.
When you are collecting produce from a farmer using the mobile app, you will be able to select the farmer’s field that you are collecting from. See example below for Agnes Mwangari Mwaura who has been with the Adjumani group since 26th November 2018. She has a two-hectare sorghum plot on which she planted seed that was distributed by the buyer who signed a contract, in this case EAML related to the brewery. The seed can be traced back to the batch.
EXAMPLE

Seed batch with batch code: “BATCH2007001” is assigned to 8 farmers on the 1st of July.
The seed batch code is added to the field under the traceability code. By filtering on the seed batch code, you can find all fields that have been initiated with the same batch. In the example below you see 8 fields have been initiated with seed from batch “BATCH2007001”, distributed by EAML.
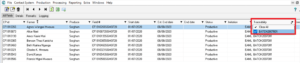
All fields with the same batch code.
Agnes Mwangari Mwaura delivered one bag of sorghum on 22nd of July 2020, for which she received a printed receipt at the field collection centre. The traceability code for that bag reads: CF1810266SGM0720.
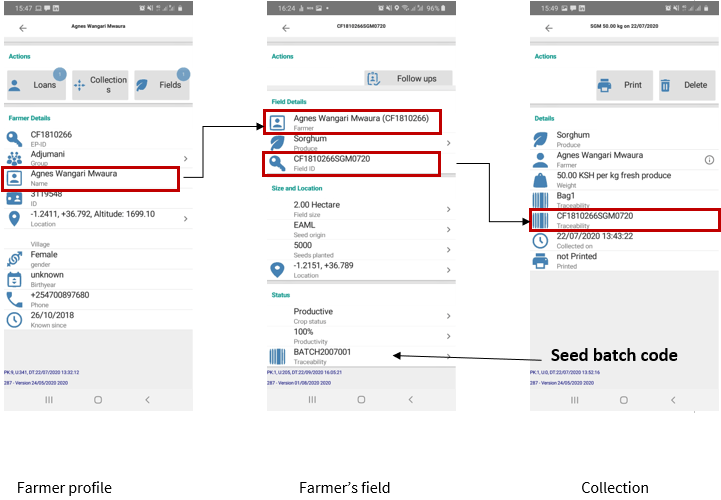
The beauty of eProd is that the systems functions perfectly offline which is essential as in most collection centres internet might be slow or even absent. As soon as the extension worker has access to internet, he or she will synchronize the data with a central database managed by the administrator of the agribusiness. From there it is possible to look up the collection data with the traceability code, see example below.
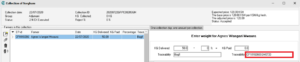
Filters
Through the M&E module in eProd you can create queries (read: filters) to select reports with information for all collections done. For example, select data for a specific day or within a specific date range. This report will show the group and farmer details, collection date, kilograms collected, traceability code of the bag (or crate, milk can, etc.), the traceability code (Field ID), product.

After a collection has been processed on the desktop application, the produce can be assigned to a Stock account. The stock account can represent a specific physical location (e.g. warehouse or silo). At that point, the collection is converted into a transaction with a Transaction ID. The transaction ID is derived from the Collection ID (see example below: 20200722GRPC00206SGM).
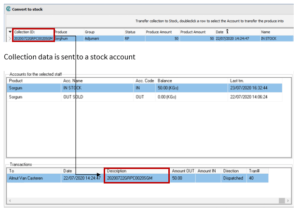
The inventory of the stock can now be managed in eProd. By linking each step in the process, a traceable supply chain is created from seed to warehouse.
Traceability and value addition
eProd’s ERP, or enterprise resources planning tool, can manage traceability from the field to the warehouse. Often additional value addition is done before the product leaves the packhouse. Matthias Grabe, Managing Director North East Africa at Buhler Limited, the Africa Division of the Buhler Group: “A miller will typically take the produce through several processing steps: sieving, destoning, sorting with gravity tables, packaging, for example. Even though the process is considered continuous, deliveries could be considered batches where the smallest batch depends on the silo size used.
The software that controls the processing steps in mill can control the batch processing in the case of advanced systems, such as those supplied by Buhler.” This impressive Swiss family owned company is globally the dominant supplier for high-end food processing equipment for grain millers, pulses, oil crops, coffee, and cocoa. eProd can be integrated with such ERPs that manage these value addition processes from warehouse to (semi) final product.
By integrating the two processes eProd can create a fully traceable supply chain and contribute to food safety in a globalized economy, while creating market opportunities for small scale farmers.
Our team will be happy to explain in more detail. Please reach out for more information or live demonstration to info@eprod-solutions.com